Laser Cutting System for Filters Made of Technical Textiles
- GOLDENLASER JMC Series CO2 Laser Cutter
- High speed, high precision, highly automated CNC laser that is equipped with Gear & Rack driven motors
Benefits of Laser Cutting Filter Press Cloth
Automatic sealing of cutting edges prevents fraying
Clean and perfect cut edges - no post-processing necessary
No fabric distortion due to contactless processing
High precision and accuracy repeatability
No tool wear - consistently high cutting quality
High flexibility in cutting any sizes and shapes - without tool preparation or tool changes
Laser Cutting Filter Press Cloth
GOLDENLASER JMC SERIES CO2 Laser Cutting Machine
Laser automatic processing flow
Our high-standard manufacturing of CO2 laser cutting machine, multi-functional expansion, configuration of automatic feeding and sorting systems, research and development of practical software... All in order to provide customers with high production efficiency, optimized production process, saving economic costs and time costs, and maximize the benefits.
Superiorities of JMC Series Cutting Laser Machine
1. Fully enclosed structure
Large format laser cutting bed with fully enclosed structure to ensure the cutting dust does not leak, suitable for operation in the intensive production plant.
In addition, the user-friendly wireless handle can realize remote operation.
High-precision Gear & Rack driving system. High speed cutting. Speed up to 1200mm/s, acceleration 10000mm/s2, and can maintain long-term stability.
- High level of precision and repeatability.
- Ensure excellent cutting quality.
- Durable and powerful. For your 24/7h production.
- Service life longer than 10 years.
3. Precision tension feeding
Auto-feeder specification:
- The width of single roller range from 1.6 meters ~ 8 meters; the maximum diameter of roll is 1 meter; Affordable weight up to 500 KG
- Auto-induction feeding by cloth inductor; Right-and-left deviation correction; Material positioning by edge control
Precision tension feeding
No tension feeder will easy to distort the variant in the feeding process, resulting the ordinary correction function multiplier;
Tension feeder in a comprehensive fixed on both sides of the material at the same time, with automatically pull the cloth delivery by roller, all process with tension, it will be perfect correction and feeding precision.
X-axis synchronous feeding
4. Exhaust and filter units
Advantages
• Always achieve maximum cutting quality
• Different materials apply to different working tables
• Independently control of the upward or downward extraction
• Suction pressure throughout the table
• Ensure optimal air quality in the production environment
According to customer requirements, a contactless ink-jet printer device and a mark pen device can be installed on the laser head to mark the filter material, which is convenient for later sewing.
Functions of ink-jet printer:
1. Mark figures and cut edge accurately
2. Number off-cut
Operators can mark on off-cut with some information such as off-cut size and mission name
3. Contactless marking
Contactless marking is the best choice for sewing. The precise location lines make subsequent work more easily.
6. Customizable cutting areas
2300mm×2300mm (90.5in×90.5in), 2500mm×3000mm (98.4in×118in), 3000mm×3000mm (118in×118in), 3500mm×4000mm (137.7in×157.4in) Or other options. The largest working area is up to 3200mm×12000mm (126in×472.4in)
Watch Laser Cutting Machine for Filter Press Cloth in Action!
Filter materials cut by laser
Filtration as an important environmental and safety control process generally sorted as gas-solid separation, gas-liquid separation, solid-liquid separation, solid-solid separation. Usually laser processing filter cloth is mainly made of technical textile.
It costs much time by traditional processing such as die cutting and CNC cutting. On one hand, traditional cutting always cause rough edges which affect next steps. On the other hand, long time cutting cause tool wear, and it cost time to replace them. Besides, die cutting need preparing die tools. But laser processing could almost avoid all these defects, processing design figures freely by very easy adjustment.
Filter materials (filter fabrics and filter mats) suitable for laser cutting:
Polyester, Polypropylene (PP), Polyurethane (PU), Polyethylene (PE), Polyamide (Nylon), Filter Fleece, Foam, Nonwoven, Paper, Cotton, PTFE, Fiberglass (fiberglass, glass fiber) and other industrial fabrics.
Technical Parameter
Laser type |
CO2 RF laser tube |
Laser power |
150W / 300W / 600W / 800W |
Cutting Area |
3000mm×3000mm (118”×118”)
|
Working table |
Vacuum conveyor working table |
Motion system |
Gear and rack driven, Servo motor |
Cutting speed |
0-1200mm/s |
Acceleration |
8000mm/s2 |
Lubrication system |
Automatic lubrication system |
Fume extraction system |
Specialized connection pipe with N centrifugal blowers |
Cooling system |
Processional original water chiller system |
Laser head |
Processional CO2 laser cutting head |
Control |
Offline controlling system |
Repeat positioning accuracy |
±0.03mm |
Positioning accuracy |
±0.05mm |
Min. kerf |
0.5~0.05mm (depending on material) |
Total power |
≤25KW |
Format supported |
PLT, DXF, AI, DST, BMP |
Power supply |
AC380V±5% 50/60Hz 3Phase |
Certification |
ROHS, CE, FDA |
Options |
Auto-feeder, Red dot positioning, Marking system, Galvo system, Double heads, CCD camera |
※ Working areas can be customized on request.
Main Components and Parts
Article Name |
Qty |
Origin |
Laser tube |
1 set |
Rofin (Germany) / Coherent (USA) / Synrad (USA) |
Focus lens |
1 pc |
II IV USA |
Servo motor and driver |
4 sets |
YASKAWA (Japan) |
Rack and pinion |
1 set |
Atlanta |
Dynamic focus laser head |
1 set |
Raytools |
Gear reducer |
3 sets |
Alpha |
Control system |
1 set |
GoldenLaser |
Liner guide |
1 set |
Rexroth |
Automatic lubricating system |
1 set |
GoldenLaser |
Water chiller |
1 set |
GoldenLaser |
JMC SERIES LASER CUTTING MACHINE RECOMMENDED MODELS
→ JMC-230230LD. Working Area 2300mmX2300mm (90.5 inch×90.5 inch) Laser Power: 150W / 300W / 600W / 800W CO2 RF Laser
→ JMC-250300LD. Working Area 2500mm×3000mm (98.4 inch×118 inch) Laser Power: 150W / 300W / 600W / 800W CO2 RF Laser
→ JMC-300300LD. Working Area 3000mmX3000mm (118 inch×118 inch) Laser Power: 150W / 300W / 600W / 800W CO2 RF Laser … … 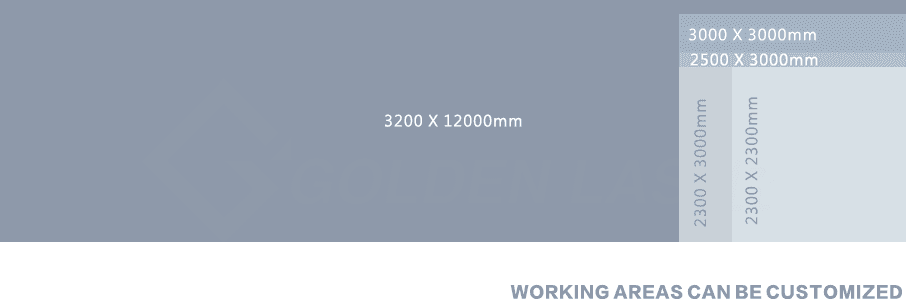
APPLICATION MATERIALS
Filtration fabrics, filter cloth, glass fiber, non-woven fabric, paper, foam, cotton, polypropylene, polyester, PTFE, polyamide fabrics, synthetic polymer fabrics, nylon and other industrial fabrics.
Laser Cutting Filter Media Samples
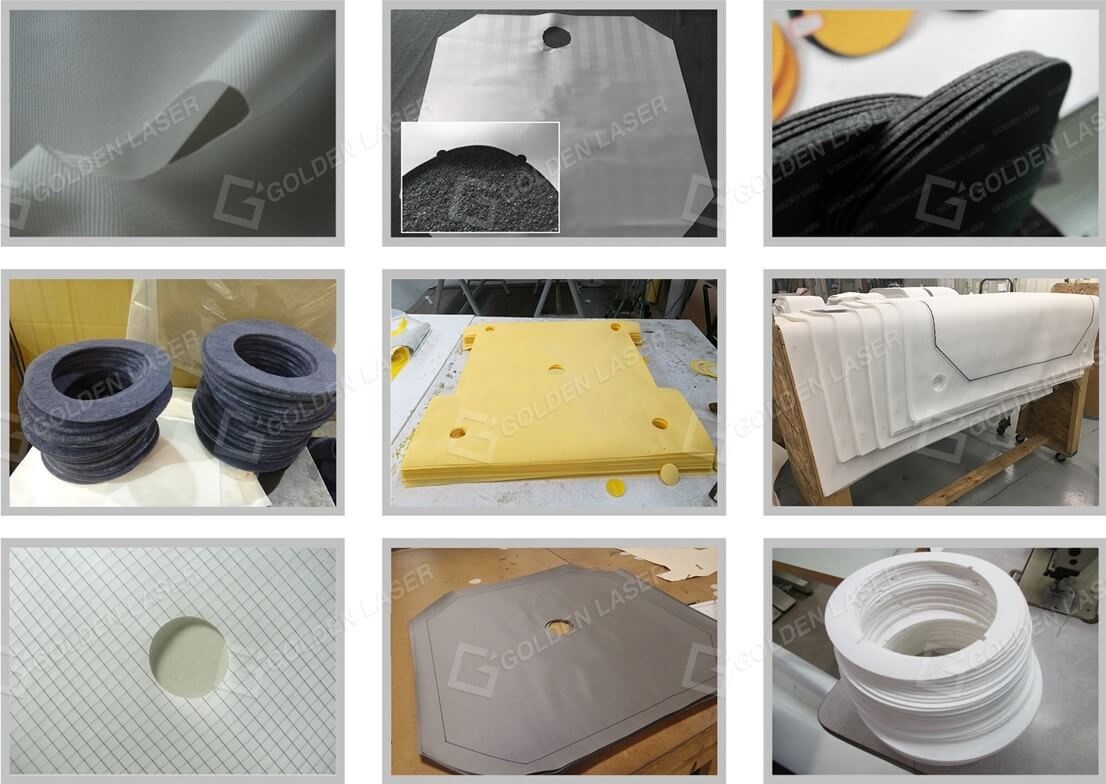
Industry Introduction
Filtration as an important environmental and safety control process, from industrial gas-solid separation, gas-liquid separation, solid-liquid separation, solid-solid separation, to daily household appliances in the air purification and water purification, filtration has been increasingly widely applied to multiple areas. Specific applications such as power plants, steel mills, cement plants and other emissions, textile and garment industry, air filtration, sewage treatment, chemical industry filtration crystallization, the automotive industry air, oil filter and home air conditioning, vacuum cleaner and so on. The main filter materials are fibrous materials, woven fabrics and metal materials, especially the most widely used fiber materials, mainly cotton, wool, linen, silk, viscose fiber, polypropylene, nylon, polyester, acrylic, nitrile, such as synthetic fibers, as well as glass fibers, ceramic fibers, metal fibers and so on. Applications are constantly expanding and filtering materials are also update, the product from the dust cloth, dust bags, filters filter barrels, filter cotton, to filter.
LASER CUTING / KNIFE CUTTING / PUNCH PROCESSING COMPARISON
|
LASER CUTING
|
KNIFE CUTTING
|
PUNCH
|
CUTTING EDGE QUALITY |
SMOOTH
|
FRAYED
|
FRAYED
|
CUT QUALITY IN THE CYCLE |
PRECISE
|
DEFORMATION
|
DEFORMATION
|
FINE DETAILS / RADIUS-FREE INNER CONTOURS |
YES
|
CONDITIONAL
|
CONDITIONAL
|
CUT EDGE SEALING |
YES
|
NO
|
NO
|
FLEXIBILITY / INDIVIDUALITY |
HIGH
|
HIGH
|
LIMITED
|
LABELING / ENGRAVING |
YES
|
NO
|
NO
|
MATERIAL DISTORTION WHEN CUTTING |
NO
(Due to non-contact)
|
YES
|
YES
|
LASER PROCESSING FLOW
3 STEPS | 1 PERSON OPERATION
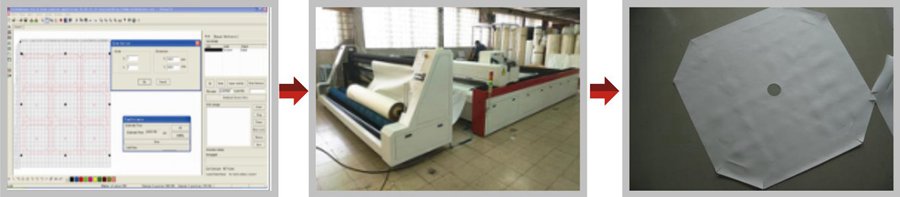
<< Read More about Filter Materials Laser Cutting Solutions